PureJet®
is the world’s most advanced Waste Gas Treatment Technology Custom Solutions to manage emissions. Including most waste gas, BTEX / VOC’s code & regulatory compliant
Technology Benefits
• PureJet takes the pressure off • PureJet uses patented Aerospace Technology • PureJet has no visible flame • PureJet has no moving parts • PureJet has industry leading performance • PJ8, PJ12, PJ18, PJ32
Engineered Solutions:
○ Large Scale Products ○ Special Projects ○ Integration ○ CFD ○ Finite Analysis
Overview
The PureJet is a family of incinerators that apply patented aerospace technologies to methane and other waste gas destruction. With its intake technology, PureJet provides industry-leading capacities and turndown ratios in a minimal footprint while utilizing no-moving parts – reducing maintenance and increasing service life.
The PureJet has numerous benefits compared to traditional incineration technologies:
✓ No moving parts
✓ High turndown ratio
✓ 99.9% complete combustion
✓ Small footprint
The system consists of a high-velocity fuel nozzle, the patented intake system, a primary burner, secondary burner and exhaust stages, and an external shroud. The system operates by ejecting waste gas directly from the nozzle and through the intake system. The intake system utilizes a combination of venturi effect and buoyancy to draw in air for combustion. The high entrainment capabilities of the intake enable an air-rich mixture to be obtained within the unit.
The critical element to the operation of PureJet is its patented intake system. Providing sufficientair to facilitate the combustion of a large amount of waste gas is a complex engineering problem. The supply of adequate air can be accomplished in many ways – most of which are either extremely complicated – or mostly ineffective. PureJet’s unique application of the venturi effect and buoyancy to entrain air allow it to achieve much higher capacities and turndown ratios than other solutions.

Model: PJ18

Model: PJ18
Operational Principles
In a stored waste gas, there is a substantial amount of stored potential energy – both chemical (due to the potential for combustion) and mechanical (due to the stored pressure relative to the atmosphere). The PureJet intake harnesses both forms of energy to drive entrainment, which provides the air for combustion within the unit. The PureJet intake utilizes a combination of the venturi effect and buoyancy to drive entrainment of the air necessary for effective combustion. First, the waste gas is ejected through the intake, the high speed and expanded gasstream entrains air into the intake. The specific geometry of the intake system enhances this entrainment maximizing the effectiveness of the system. Once the unit is in operation, the performance of the PureJet is enhanced by the tendency of the hot combustion gases to rise. This buoyancy effect further improves entrainment through the intake, thereby supplying more oxygen for combustion. Since entrainment is, by definition, a mixing process, the inlet simultaneously provides the primary combustor with a well-mixed air-waste gas mixture.
The mechanics of this process are often not obvious. One helpful way is through analogy. Overall, the PureJet intake operates through an efficient conversion from stored potential energy to the energy required for entrainment and waste gas destruction. A useful moving-parts analogy is the process shown in Fig.
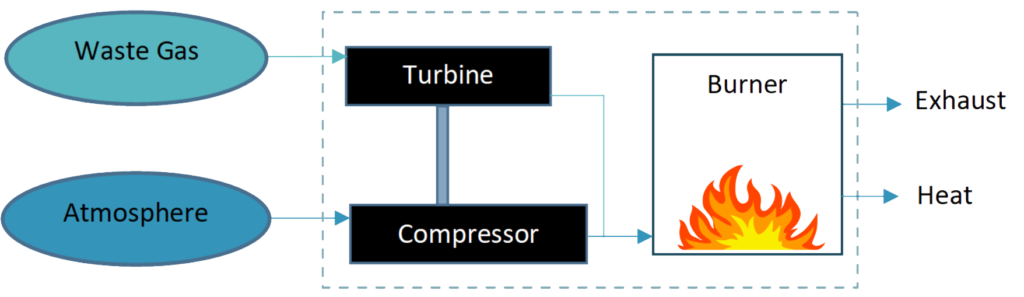
Unit Capacity Ranges
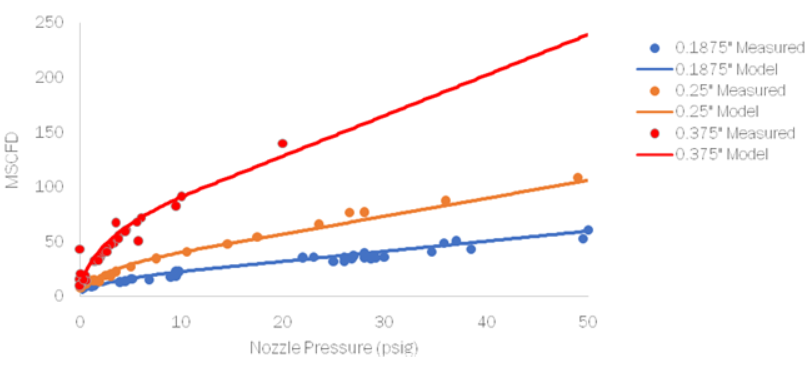
Unit Temperatures
Typically, PureJet units maintain temperatures below 1000oC on internal components when they are operating on-design. The interior unit temperature is a complicated relationship between nozzle size, pressure, and the intake and burner geometries. PureJet unit temperatures are controlled by (a) selecting the correct PureJet unit for an intended capacity, and (b) careful selection of nozzle size based on available pressures. An example of field data for a PureJet unit operating on 96.5% methane gas.